China Embraces Small-Batch Customized Hardware Products
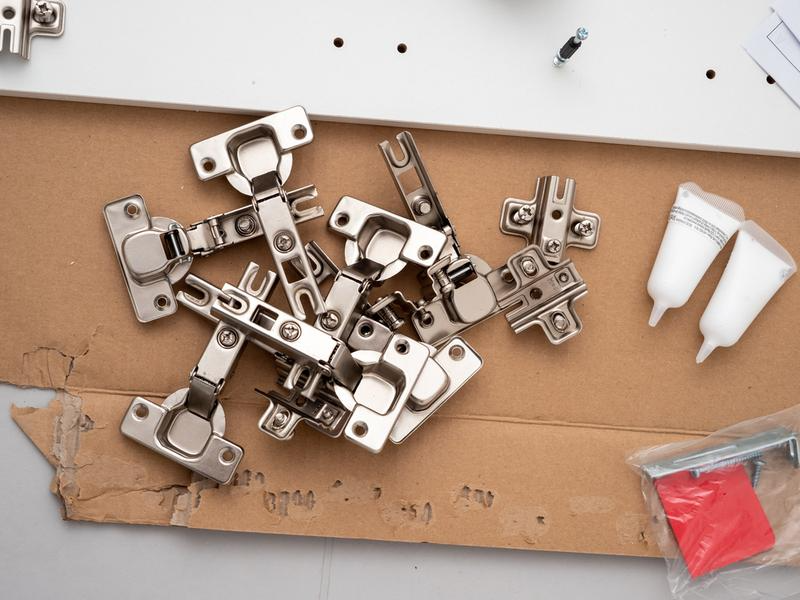
China Embraces Small-Batch Customized Hardware Products
China’s small and medium-sized enterprises (SMEs), numbering over 42 million and constituting 99.8% of the nation’s total enterprises, contribute significantly to the country’s Gross Domestic Product (GDP), with 60% of the share. Despite this, the journey towards smart manufacturing is a long and arduous one.
The manufacturing industry has shifted from mass production to market segmentation and competition based on customer needs. Producing a variety of personalized products has become an inevitable choice. Most manufacturing companies, especially SMEs, are engaged in multi-variety, small-batch production, switching tasks multiple times a day.
This production model leads to short product lifecycles, a vast array of products and components, and complex, lengthy supply chains, causing significant management challenges and high operational costs.
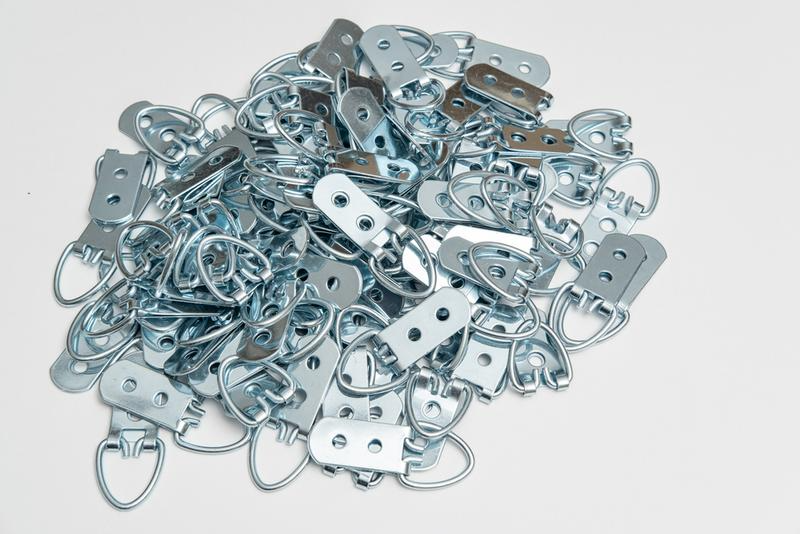
Managing Custom Orders
The hardware industry is highly susceptible to market fluctuations, with frequent production adjustments and changes in customer orders. Emergency orders often disrupt existing production plans. Most manufacturing companies use Just-In-Time (JIT) production methods, resulting in short order cycles and delivery delays. With varying order cycles, quantities, and logistics pickup methods, the information management becomes exceedingly complex, leaving supervisors in a constant state of “firefighting.”
To address these challenges, Chinese companies are:
- Utilizing Supplier Relationship Management (SRM) to issue production orders and create corresponding plans, minimizing urgent order changes to reduce excessive waste.
- Organizing standard or common components and integrating them into Product Lifecycle Management (PLM) systems to improve the efficiency of craft compilation.
- Integrating Enterprise Resource Planning (ERP) and Manufacturing Execution System (MES) to manage production materials precisely, adjusting production plans swiftly in response to order changes, and shortening production cycles.
- Sales departments are integrating third-party logistics information to effectively control on-time delivery rates.
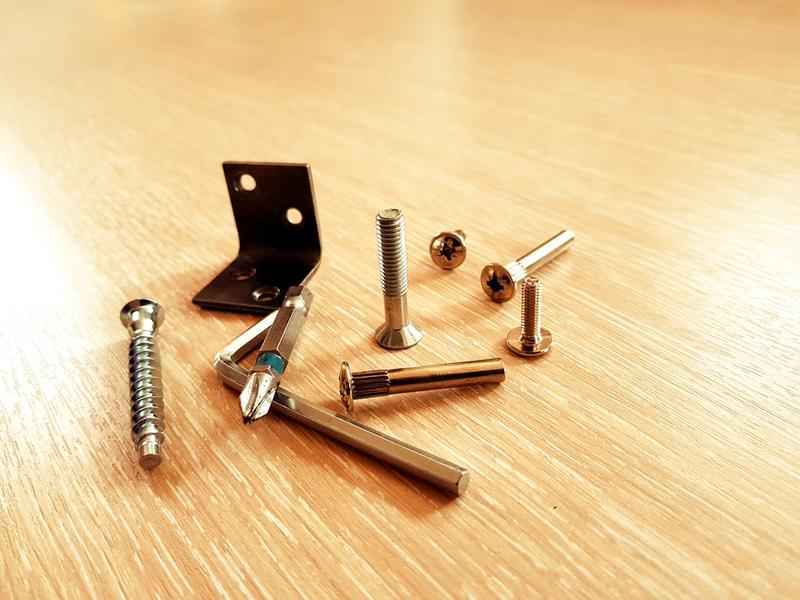
Scheduling Diverse Categories
Many important customer orders are small-batch, multi-variety types, leading to additional demands that cannot be mass-produced. Planning departments often resort to manual Excel methods for production scheduling. Once the schedule is set, Supervise the execution status becomes difficult: What are the in-progress orders? What is their status? Which processes have not started or finished as planned? How many qualified and unqualified products are there? The disconnect between planning and execution relies on constant movement to gather information.
Chinese companies are solving the problem of managing a multitude of varieties and difficult scheduling by:
- Establishing a PLM system to manage the entire lifecycle of products, setting up a standard R&D system, and Unified management and presentation product configurations, structures, assembly relationships, and manufacturing processes, improving the efficiency of craft compilation.
- Implementing MES for precise control on the shop floor, establishing common components, considering the possibility of a super Bill of Materials (BOM), and effectively shortening production cycles.
- Deep integration of ERP and MES systems for real-time monitoring, control, statistics, and analysis of all production details, with shop floor dashboards displaying real-time data to optimize capacity.
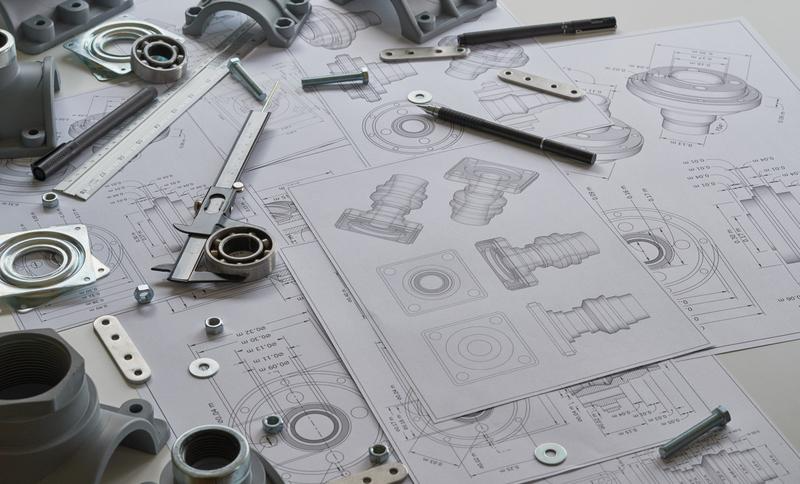
Responding to Design Changes
Most orders are for non-standard product designs, which go through numerous stages including design, prototyping, and production. Design changes are frequent, production time is tight, accuracy is untraceable, and cost control is challenging: Are there any inflated working hours or waste? Which orders are consuming high working hours?
Chinese companies are addressing these issues by:
- Utilizing equipment networking and contactless sensing to collect information on people, machines, materials, methods, and environment in the workshop, avoiding data errors and cost waste caused by manual reporting.
- If conditions permit, applying RFID technology to existing production resources to reflect real-time material status and provide accurate, transparent, and reliable information for production planning, precisely calculating production costs.
Chinese hardware companies have evolved from small to large-scale operations, transitioning from traditional to modern hardware, relying on technological progress and embracing the path of technology-driven industrial parks and businesses.
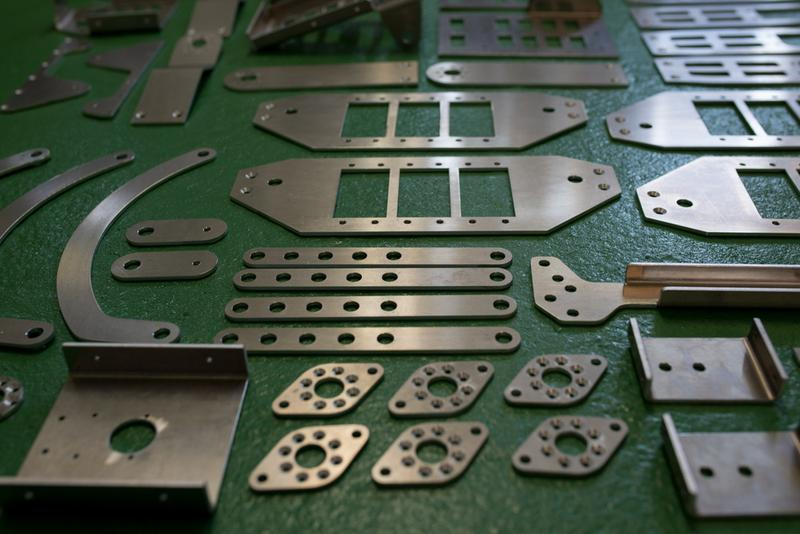
Integrating Resources in the Hardware Industry
How can the hardware industry integrate resources to adapt to the trends of economic globalization? The internet’s information integration capabilities have provided possibilities for industry alliances. The emergence of industry e-commerce platforms has offered a space-transcending marketplace for many businesses, and online sales have become a trend. In 2019, industry B2B websites dominated the list of China’s most commercially valuable websites, with hardware industry sites leading the way.
In regions concentrated with hardware industries, such as Yongkang in Zhejiang and Foshan and Zhongshan in Guangdong, traditional hardware manufacturers are gradually achieving forward and backward integration. Factories that once only produced hardware spare parts are now involved in the manufacturing of large-scale machinery equipment. Enterprises in a region have also achieved strategic integration from raw material processing to spare part supply to finished product manufacturing.
Hardware manufacturing companies are placing greater emphasis on product R&D and technological innovation, which has promoted the industrial upgrading of hardware enterprises. “Large-scale hardware manufacturing” has become a trend in industrially concentrated areas.