Overcoming Challenges in Sourcing Custom Furniture Hardware Components
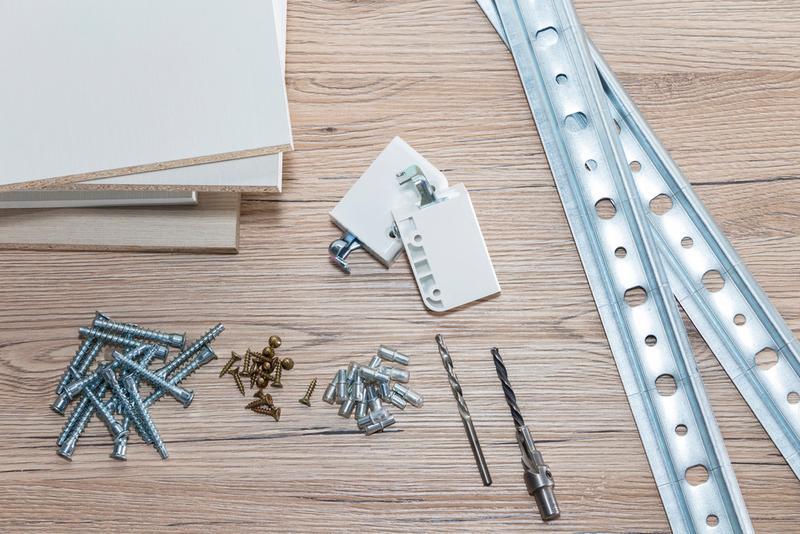
The Challenges of Sourcing Custom Furniture Hardware Components
Just like furniture styles, furniture hardware components also have best-sellers and new arrivals. Commonly used hardware for home furnishings typically consists of hundreds or even thousands of individual parts. These parts might include basic standard hardware like bolts, nuts, hinges, sofa legs, springs, and more. They could also be more intricate and specialized, such as smart furniture components, non-standard custom items, industrial control sensors, lead screws, rails, and other precision parts. Each component has specific applications and usage requirements, and its quality and stability directly impact the performance and longevity of the final product.
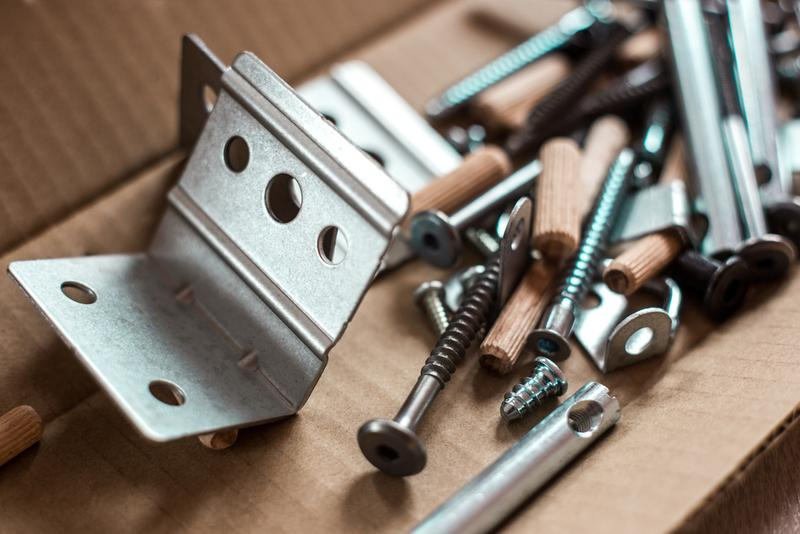
Challenges in Sourcing Custom Furniture Hardware
The furniture hardware market faces several challenges. From the supply side, different products often require distinct manufacturing processes and techniques. As a result, suppliers typically specialize in specific product types, leading to a limited range of available components. From the demand side, China, as a manufacturing powerhouse, sees a huge demand for furniture hardware components from various equipment manufacturers every year. However, this demand is highly fragmented. Here are the key pain points for buyers:
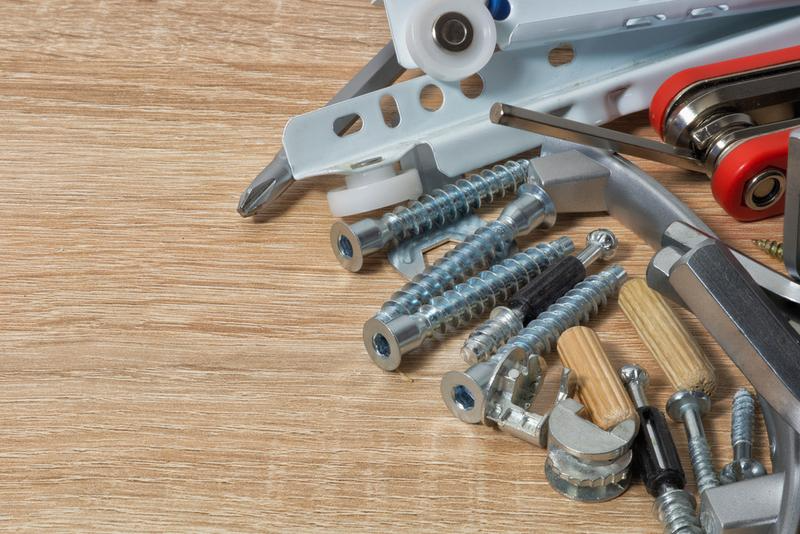
1. Overwhelming Non-Standard Options and SKU Selection
Due to the limited range of products offered by each supplier, procurement costs and lead times increase. Additionally, many furniture hardware components do not have standardized models, and product specifications can vary. This makes it time-consuming and difficult for procurement teams to find the right parts, match models, and communicate effectively, leading to sourcing difficulties.
2. Long Customization Lead Times and Uncertain Quality
For custom non-standard hardware parts, especially during peak seasons, scattered orders can be delayed by bulk orders, pushing back delivery times. Even if a single part is delayed, it can halt or disrupt the assembly process. Furthermore, unstable supplier quality control and delivery schedules may result in products that don’t meet actual needs, leading to delivery issues and customer dissatisfaction.
3. Lack of Price Transparency and Bargaining Power
In China, numerous small and medium-sized equipment manufacturers have decentralized procurement needs. Due to limited purchase volumes, these companies often lack bargaining power, resulting in high procurement costs. The production cost of furniture hardware components is closely tied to production scale and methods. For example, parts produced through mold-making or mass production are significantly cheaper. However, the information asymmetry between buyers and suppliers causes significant price disparities for the same components.
4. Difficulty Accessing Reliable Chinese Factories
If you are looking to find a Chinese factory that manufactures hardware, where do you start? Most Chinese factories focus on OEM manufacturing and often have long histories, having attended international trade shows early in their establishment. However, many businesses still rely heavily on relationships to connect with potential clients. This is the standard operating model for most Chinese companies.
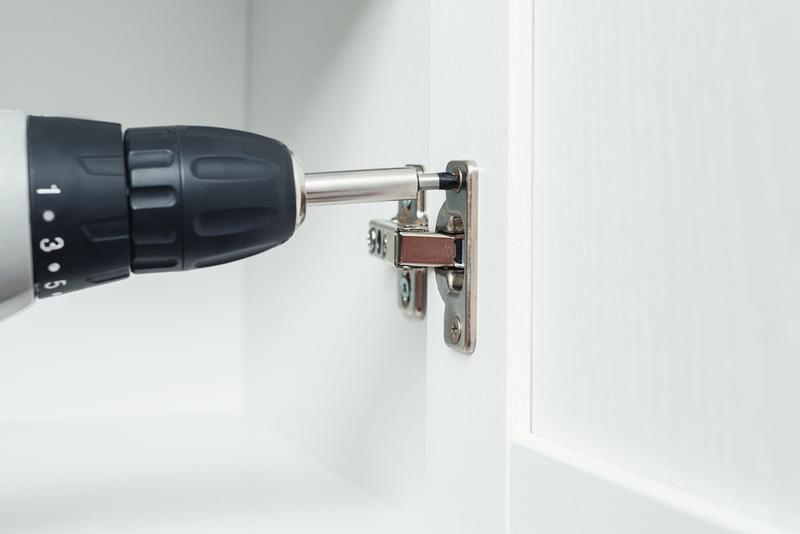
Typically, business owners build relationships with procurement managers, general managers, or even owners of client companies, securing orders through these connections. While some companies succeed in attracting clients due to their excellent capabilities, many suppliers lack bargaining power. In most cases, clients set the prices, as many suppliers cannot accurately price their products. This often leads to suppliers relying on rough estimates for pricing. Nonetheless, the furniture hardware industry remains profitable, as long as there are no major quality issues with the products.